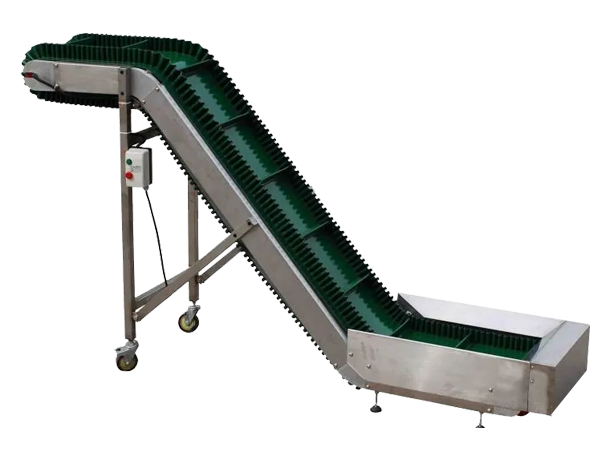
Cleated Belt Conveyors
Transport products using belts with evenly spaced baffles or bumps that help grip and position products to prevent them from slipping or falling off the conveyor, especially when conveying products uphill or around curves.
High guard: 60-200mm
Minimum horizontal baffle spacing: 100-250mm
Speed: 0-20m/min (adjustable)
Load Capacity: 0KG-100KG
Introduction of Cleated Belt Conveyors
Cleated belt conveyors, also called corrugated cleated belt conveyor, use belts with evenly spaced baffles or protrusions to transport products. These baffles help to grip and position the products, preventing them from slipping or falling off the conveyor, especially when conveying products up inclines or around curves.
Cleated belt conveyors are versatile and can handle a wide range of materials, including loose, granular, or bulky items that would otherwise be difficult to transport on a standard belt conveyor.
Incline Capability: They are particularly effective for conveying materials up inclines or declines, where maintaining material position is crucial.
Types of Cleated Belt Conveyors
1. According to the appearance
Horizontal cleated belt conveyors: These conveyors are used for horizontal transport of materials where additional grip is required to prevent material slippage.
Incline cleated belt conveyors: These conveyors are designed to transport materials up inclines or declines. The cleats help to prevent materials from slipping back on an incline.
Z-Shaped cleated belt conveyors: These conveyors have a zig-zag or Z-shaped configuration, allowing for vertical lift capabilities along with horizontal transportation.
2. According to the application
Aluminum cleated belt conveyors: mainly made of aluminum, suitable for environments with humid or corrosive substances.
Sanitary cleated belt conveyors: conveyors are usually made of stainless steel, easy to clean and maintain, and corrosion-resistant. The belts are usually made of food-grade rubber or PVC, which are resistant to high and low temperatures and can withstand gap cleaning and disinfection.
Application
Cleated belt conveyors are versatile and find application in various industries where the cleats play a crucial role in material handling. The cleats on these conveyors provide added grip and control over the movement of materials, making them suitable for specific applications that require enhanced conveying capabilities. Here are some key applications where the cleated feature of belt conveyors plays a significant role:
Food Processing: In the food industry, cleated belt conveyors are used for applications where products need to be elevated or where there are inclines involved. Sanitary cleated belt conveyors are especially important in food handling to maintain cleanliness and hygiene standards.
Agriculture: Cleated belt conveyors are used in agriculture for handling crops, seeds, and other agricultural products that require secure transportation, especially on inclines.
Recycling: In recycling facilities, cleated belt conveyors are utilized to transport sorted materials such as plastics, paper, or metals, ensuring efficient material flow and separation.
Mining and Quarrying: Cleated belt conveyors are employed in the mining industry to transport ores, rocks, and other materials over long distances and varying terrain.
Manufacturing: Cleated belt conveyors are used in manufacturing plants for handling products on assembly lines, moving items between workstations, or managing the flow of materials during production processes.
Video
Structure of Cleated Belt Conveyors
Cleated belt conveyors are composed of corrugated sidewall belts, base belt diaphragms, machine head drive rollers, drive devices, reversing pressure rollers, sidewall rollers, rappers, etc.
Sidewall: designed to be corrugated to prevent the material from slipping and falling.
Diaphragm: The main function is to support materials, which can be divided into two categories: fixed type and detachable type.
The ribs and the diaphragm are connected with the base tape by the method of secondary vulcanization, which has a high connection strength.
Technical Parameters
bandwidthB(mm) | 300 | 400 | 500 | 650 | 800 | |||||||||
sidewall height(mm) | 40 | 60 | 60 | 80 | 80 | 120 | 120 | 160 | 120 | 160 | 200 | 240 | ||
Partial conveying inclination conveying amountQ3/h | 30° | 15 | 14 | 20 | 34 | 46 | 71 | 104 | 120 | 128 | 157 | 195 | 235 | |
45° | 11 | 10 | 14 | 26 | 35 | 57 | 83 | 97 | 102 | 127 | 157 | 195 | ||
60° | 8 | 7 | 10 | 18 | 25 | 40 | 58 | 69 | 72 | 90 | 112 | 142 | ||
90° | 4 | 4 | 5 | 10 | 13 | 21 | 31 | 37 | 38 | 48 | 60 | 76 | ||
Dimensions | Head wheel center heightH2/h(MM) | 350-100 | 1100-2000 | 1300-2000 | 1300-2000 | |||||||||
Tail wheel center heightH2/h(MM) | 335 | 330-490 | 600 | 600 | 600-800 | |||||||||
Middle section belt heightH2/h(MM) | 450 | 500-700 | 760-800 | 800-850 | 800-1115 | |||||||||
Middle foot widthB2/h(MM) | 480 | 580 | 870 | 1020 | 1220 | |||||||||
bandwidthB(mm) | 1000 | 1200 | 1400 | |||||||||||
sidewall height(mm) | 120 | 160 | 200 | 240 | 160 | 200 | 240 | 300 | 160 | 200 | 240 | 300 | 400 | |
Partial conveying inclination conveying amountQ3/h | 30° | 172 | 216 | 267 | 327 | 275 | 331 | 419 | 466 | 319 | 395 | 500 | 564 | 794 |
45° | 137 | 175 | 216 | 271 | 222 | 267 | 347 | 384 | 258 | 318 | 414 | 465 | 680 | |
60° | 96 | 124 | 153 | 197 | 158 | 190 | 253 | 178 | 184 | 226 | 302 | 337 | 524 | |
90° | 51 | 66 | 83 | 106 | 85 | 102 | 136 | 149 | 98 | 121 | 162 | 180 | 281 | |
Dimensions | Head wheel center heightH2/h(MM) | 1400-2000 | 1600-2000 | |||||||||||
Tail wheel center heightH2/h(MM) | 600-800 | 800-1000 | 800-1200 | |||||||||||
Middle section belt heightH2/h(MM) | 800-1200 | 1050-1500 | 1050-1700 | |||||||||||
Middle foot widthB2/h(MM) | 1440 | 1690 | 1890 |
Features and Benefits
Enhanced Grip: The cleats provide additional grip on the belt, preventing materials from slipping or falling off, even when the conveyor is inclined.
Versatility: Cleated belt conveyors are versatile and can handle a wide range of materials, including loose, granular, or bulky items that would otherwise be difficult to transport on a standard belt conveyor.
Incline Capability: They are particularly effective for conveying materials up inclines or declines, where maintaining material position is crucial.
Prevent Spillage: Cleats help in containing materials within the conveying path, reducing spillage and improving overall efficiency.
Customization: Cleated belt conveyors can be customized with different cleat heights, spacing, and patterns to suit specific material handling requirements.
Durability: They are typically built to be durable and withstand heavy loads and harsh operating conditions.
Cleated Belt type selection
There are many different types of belt materials for cleated belt conveyors, and it is important to choose the right belt material for your specific application. Here are some common types of belt materials for cleated belt conveyors:
Rubber belt: wear-resistant, oil-resistant, good elasticity, suitable for various environments, moderate price, widely evaluated in food, beverage, logistics and other industries.
PVC belt: acid and alkali resistant, corrosion-resistant, easy to clean, suitable for environments with high hygiene requirements, suitable for food processing, light material transportation and other occasions with high cleanliness requirements.
PU belt: wear-resistant, grease-resistant, heat-resistant, suitable for heavy material transportation and high wear resistance requirements.
Solutions by Industry