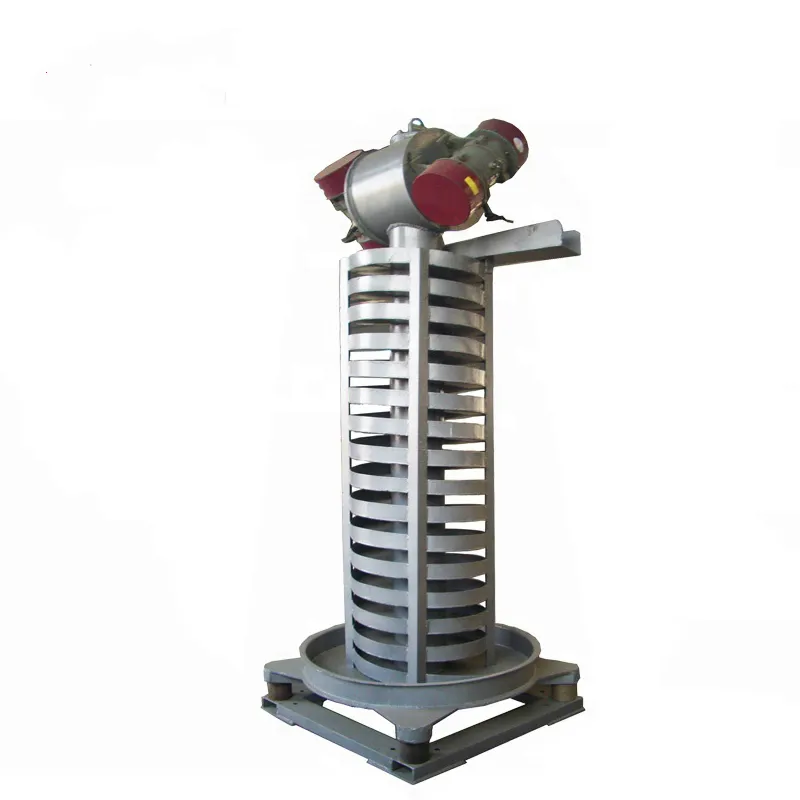
Bulk Material Vibrating spiral Conveyor
The combined amplitude of the two vibration motors transports the material upward or downward along the spiral conveyor trough. During the movement, the material can also be dried or cooled at the same time.
Conveyor trough diameter: 300-900mm
Height: ≤6 meters
Conveying capacity: 3-5 tons/hour
Power: 2* (0.4-3)kw
Application: It is mainly used to lift bulk materials such as powder, granules, and pellets.
Introduction of Bulk Material Vibrating spiral Conveyor
Bulk material vibrating spiral conveyor is mainly used to convey granular, powdery or small block materials vertically upward. It uses the principle of vibration to make the materials jump upward in the inclined conveying trough, thereby achieving continuous conveying.
Bulk material vibrating spiral conveyor can be used to cool, dry and lift materials. It is widely used in plastics, chemicals, mining and other processing industries. The lifting height can reach 6 meters and the maximum conveying capacity is 8t/h. It can be adjusted according to the specific operation needs of customers.
Use of bulk material vibrating spiral conveyor
1.Material conveying: Bulk material vibrating spiral conveyor can lift materials from the ground to a high place, and is suitable for various industrial scenarios, such as mining, metallurgy, machinery, building materials, chemicals, rubber, medicine, electricity, grain and food industries.
2.Drying function: While lifting the material, the material is fully in contact with the air through vibration, which plays a role in heat dissipation and cooling, and completes the drying of the material.
3.Cooling function: For high-temperature materials, it can quickly cool them down, and is suitable for materials that need cooling treatment.
Working principle of bulk material vibrating spiral conveyor
Bulk material vibrating spiral conveyor is a device used to vertically convey bulk materials such as particles or powders. Its working principle is as follows:
Vibration source: The vibration source is usually provided by a vibration motor. The vibration motor transmits the vibration generated by the body to the working surface of the conveyor through the exciter.
Lifting: When the vibration motor is started, the conveying trough will be subjected to vertical vibration force, and the particles or powder materials will vibrate upward.
Material transportation: Under the action of vibration, the material will show creeping motion and move upward along the working surface of the elevator.
Unloading: When the material reaches the target height or reaches the set position, the material can be unloaded through the set unloading port to complete the vertical conveying process.
Application of Bulk Material Vibrating spiral Conveyor
1. Conveying and grading of powdered materials
Food industry: conveying powdered materials such as flour, starch, milk powder, etc., to achieve metering and batching.
Chemical industry: conveying various chemical powders, such as calcium carbonate, titanium oxide, etc., and can be combined with heating or cooling devices for temperature control.
Building materials industry: conveying powdered materials such as cement and gypsum, and can add water for mixing.
2. Conveying and cooling of granular materials
Plastic industry: conveying plastic particles, and combining with cooling devices to achieve rapid cooling. In the plastic extrusion molding process, it is used to convey cooled plastic particles.
Mining industry: conveying mineral powder, coal powder, etc., and can be combined with screens for grading.
Metallurgical industry: conveying metal powder, and can be combined with heating devices for preheating.
4. Conveying under special working conditions
High-temperature materials: conveying high-temperature ash and high-temperature materials requires the use of high-temperature resistant materials.
Corrosive materials: conveying corrosive materials such as acidic and alkaline materials requires the use of corrosion-resistant materials.
Flammable and explosive materials: conveying flammable and explosive materials requires explosion-proof measures.
Videos
Advantages of Bulk Material Vibrating spiral Conveyor
1. Space saving: Through vertical conveying, the equipment occupies less ground space, which is suitable for factories or warehouses with limited space.
2. Efficient conveying: It can achieve efficient and continuous conveying, which is suitable for large-scale production needs and improves overall production efficiency.
3. Gentle handling and reduced material damage: The vibration conveying mechanism reduces friction and impact between materials, reduces the risk of material breakage, and is particularly suitable for handling fragile or sensitive materials.
4. Strong flexibility: It can handle a variety of bulk materials, including powders, granules and block materials, and is widely used in different industries.
5. Prevent material agglomeration: The vibration mechanism can effectively prevent the agglomeration of materials during the conveying process and ensure the smooth flow of materials.
Technical parameters of Bulk Material Vibrating spiral Conveyor
Model | Lifting Capability(t/h) | Diameter of spiral chute(mm) | Lifting height(m) | Speed(rpm) | Double amplitude(mm) | Power(kw) |
DZC300 | Up To 1.0 | 300 | ≤2.0 | 960 | 6-7 | 2*0.4 |
DZC500 | Up To 2.0 | 500 | ≤3.0 | 960 | 6-8 | 2*0.75 |
DZC550 | Up To 3.0 | 550 | ≤3.5 | 960 | 6-8 | 2*1.5 |
DZC600 | Up To 3.0 | 600 | ≤4.0 | 960 | 6-7 | 2*1.5 |
DZC800 | Up To 4.0 | 800 | ≤4.5 | 960 | 6-8 | 2*2.2 |
DZC850 | Up To 4.0 | 850 | ≤5.0 | 960 | 6-9 | 2*2.2 |
DZC900 | Up To 3.5 | 900 | ≤6.0 | 960 | 6-9 | 2*3.0 |
DZC950 | Up To 4 | 950 | ≤8.0 | 960 | 6-9 | 2*3.7 |
Structure of Bulk Material Vibrating spiral Conveyor
The structural design of bulk material vibrating spiral conveyor usually includes several key components to ensure its efficient and stable operation. The following are its main structural parts:
1. Casing: usually made of wear-resistant and corrosion-resistant materials such as stainless steel or carbon steel to ensure the durability and safety of the equipment.
2. Vibration device: The motor that provides power is usually equipped with an eccentric wheel or vibrator.
3. Lifting trough: usually in a vertical or inclined state, with a smooth inner wall design to reduce the friction and resistance of the material.
4. Feeding port: set at the bottom or side of the lifting trough, the material enters the lifting trough through here, usually designed in a funnel shape to facilitate the inflow of materials.
5. Discharging port: located at the top of the lifting trough, the material is discharged through this port after being lifted to a certain height, and the design needs to ensure smooth outflow of the material.
6. Support structure: The frame structure that supports the entire elevator is usually made of steel to ensure the stability and load-bearing capacity of the equipment.
7. Vibration reduction device: It may be equipped with a shock reduction device to reduce the impact of vibration on the equipment foundation and extend the service life of the equipment.
Solutions by Industry