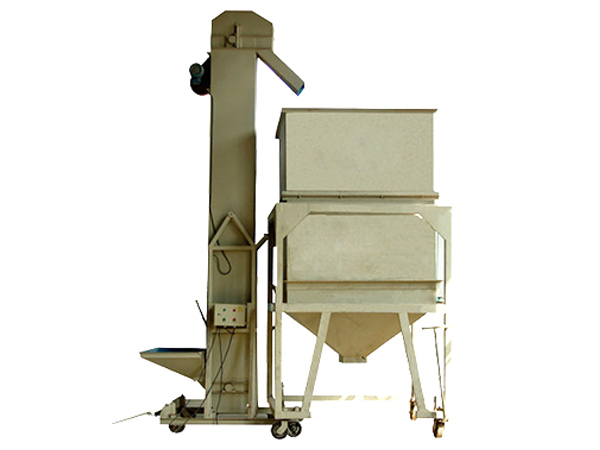
Dry powder mortar bucket elevator
A dry powder mortar bucket elevator is a specialized type of vertical conveyor system designed to efficiently lift and transport dry powder mortar materials within a production facility.
Type: Belt/Chain
Material particle size: 25-70mm
Lifting capacity: 5.4-40 tons/hour
Lifting height: ≤15 meters
Lifting speed: 1.4-2 m/s
Application: Elevating mortar mix from storage silos to mixing stations.Transporting mortar mix between different processing stages, such as sieving or packaging lines.
Introduction of Dry powder mortar bucket elevator
Dry powder mortar bucket elevator is used in dry mortar production lines to lift materials from the ground to storage bins or transport them to the next process. It is suitable for transporting dry mortar raw materials (including cement, lime, gypsum, sand, adhesives, etc.), additives (including various additives, modifiers, pigments, etc.) and finished dry mortar.
Dry powder mortar bucket elevator usually includes functions such as closed buckets, dust removal systems and smooth inner surfaces to prevent material loss and ensure efficient and clean transportation of mortar.
Types of Bucket Elevator
For different types of dry mortar, it is crucial to choose the right bucket elevator:
1. Fine powder (such as cement, gypsum): Chain bucket elevator is recommended, which has good sealing and is not easy to leak, suitable for conveying fine powder.
2. Granular material (such as sand, aggregate): Plate chain bucket elevator is recommended, which has strong carrying capacity and is suitable for conveying granular material.
Working Principle
The working process of a dry powder mortar bucket elevator is similar to that of a standard bucket elevator. Here are the key steps involved:
Loading: The dry powder mortar is loaded into the buckets at the bottom of the elevator. This can be done manually or through an automated feeding system that transfers the mortar into the buckets.
Bucket Lifting: Once the buckets are loaded, the elevator's motor or drive system is activated. It starts moving the buckets vertically upwards, lifting the dry powder mortar along with them. The buckets are securely attached to a continuous looped belt or chain, which moves them in an endless loop.
Vertical Transport: As the buckets move upwards, they carry the dry powder mortar to the desired height or level. The buckets are designed to prevent spillage and ensure the mortar remains contained during the lifting process.
Discharge: When the buckets reach the desired height or level, they reach a discharge point where the dry powder mortar needs to be released. At this point, the buckets tip or tilt, allowing the mortar to slide out of the buckets and onto the designated receiving area or equipment.
Return: After the mortar is discharged, the empty buckets continue their movement, descending to the bottom of the elevator using the return side of the looped belt or chain. They are then ready to be loaded again for the next cycle.
Application
Dry mortar bucket elevators have a wide range of application scenarios in the construction industry and mortar production fields. The following are the main application scenarios of dry mortar bucket elevators:
1. Mortar production plant: The dry mortar bucket elevator is the key equipment in the mortar production plant. It is used to transport dry mortar vertically from one processing stage to another, for example from a mortar mixer to packaging equipment, storage bins or transport vehicles. Bucket elevators can efficiently and continuously transport mortar vertically, reducing manual handling and improving production efficiency.
2. Construction site: At the construction site, dry mortar needs to be lifted vertically from the ground or storage area to high-rise buildings or construction locations. The dry mortar bucket elevator can meet this demand and transport the mortar quickly and efficiently to the location where construction is required, reducing the workload of manual handling and improving construction efficiency.
3. Mortar storage and logistics: Dry mortar bucket elevators are also widely used in the fields of mortar storage and logistics. It vertically lifts dry mortar from a warehouse or storage facility to a loading area or transport vehicle for loading and transportation. By using dry mortar bucket elevators, efficient mortar storage and logistics operations can be achieved, labor costs can be reduced, and operating efficiency can be improved.
Videos
Advantages
1. High lifting efficiency: Dry powder mortar bucket elevator can continuously carry out the lifting operation, and the lifting height is relatively large, which effectively improves the work efficiency.
2. Stable operation: Dry powder mortar bucket elevator adopts a chain transmission structure, which is stable in operation and low in noise.
3. Simple structure: The structure of the dry powder mortar bucket elevator is relatively simple and easy to maintain.
4. Wide range of applications: Dry powder mortar bucket elevator is suitable for various construction sites, such as concrete mixing stations, cement warehouses, mortar mixing stations, etc.
Technical parameters
Model | Large feed sizemm | Hopper | lift heightm | Lifting capacity (m3/h) | Hoist weight | ||
Bucket distancemm | WidthMM | CapacityL | |||||
TB250 | 90 | 200 | 250 | 3 | 5-40 | 25 | Check and determine according to the specific vertical bucket elevator ordering general drawing |
TB315 | 100 | 200 | 315 | 6 | 46 | ||
TB400 | 110 | 250 | 400 | 12 | 75 | ||
TB500 | 130 | 320 | 500 | 25 | 95 | ||
TB630 | 150 | 400 | 630 | 50 | 148 | ||
Note: The maximum conveying capacity in the table is calculated according to the filling factor ψ-0.8, which is for reference only. |
How to choose dry mortar bucket elevator
1. Bucket design: The bucket in a dry mortar elevator may be specially designed to handle mortar powders that are finer and lighter than rice grains. This may involve smoother barrel walls to prevent material buildup and ensure proper discharge.
2. Material selection: Stainless steel is a common choice because it is durable, hygienic and easy to clean. However, for some mortar mixtures, other materials such as wear-resistant carbon steel may be suitable depending on the specific composition of the mortar.
3.Capacity: Choosing the right elevator size is crucial to meet the required transport capacity for your mortar production facility.
4. Dust control: Due to the finer nature of dry mortar, the dust control function may be more important. This may involve an enclosed enclosure with a dust seal or integration with a dust collection system.
Systematic solution
1. The position of bucket elevator in the production line
Raw material transportation: lift various raw materials (such as cement, sand, admixtures, etc.) from the ground to the storage bin or batching system.
Finished product transportation: lift the produced dry mortar to the packaging machine or storage bin.
Return material transportation: lift the waste or return material in the production process to the mixing system.
The following is the configuration of a typical dry mortar bucket elevator production line:
1. Raw material storage system: used to store various raw materials, such as cement, sand, gypsum, additives, etc.
2. Measuring system: accurately measure the weight of various raw materials to ensure the accuracy of the formula, and automatically adjust the amount of each raw material according to the formula requirements.
3. Mixing system: such as a ribbon mixer or a forced mixer, used to mix all raw materials evenly to ensure the quality of mortar.
4. Bucket elevator: used to lift the mixed dry mortar to the packaging or storage equipment, usually in a vertical or inclined design.
5. Storage system: used to store the lifted dry mortar for subsequent packaging and distribution.
6. Packaging system: Pack the dry mortar into bags, usually equipped with weighing and sealing functions.
7. Control system: Equipped with a PLC control system to monitor the operating status of the entire production line, record data and alarm for faults.
8. Dust removal equipment: Prevent dust pollution generated during the production process and ensure factory environmental hygiene.
Waste gas treatment system: Treat waste gas generated during the production process in accordance with environmental protection standards.