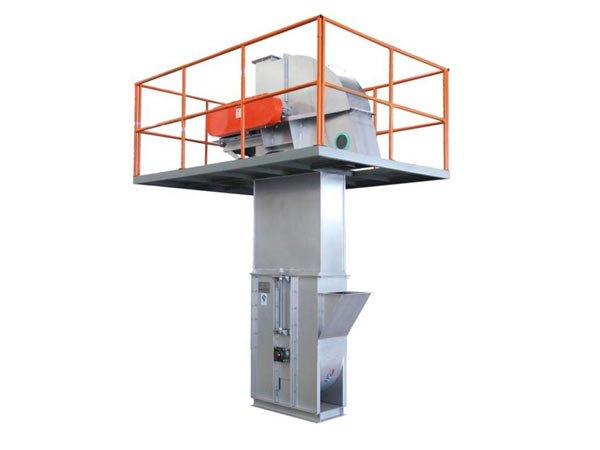
bucket elevator
It consists of a series of buckets attached to a belt or chain that move continuously in a cyclic manner, capable of moving vertically and transporting materials between different heights.
Maximum size of material: 25-45mm
Lifting height: 40 meters
Lifting capacity: 15-800 cubic meters per hour
Application: A wide range of free-flowing materials with different characteristics can be handled. Lightweight, fragile, heavy and abrasive materials can all be transported using bucket elevators.
Product introduction of bucket elevator
Bucket elevator, also called bucket elevator conveyor, is a conveying system that vertically lifts bulk materials such as grain, fertilizer and other granular or powdered materials. It consists of a bucket connected to a chain or belt that rotates around a sprocket or pulley, allowing the bucket to move vertically and transport materials between different heights.
Bucket elevators can handle a variety of materials, from grains and powders to larger bulk items. Capacity varies depending on the design. Buckets are usually made of materials such as plastic, metal or rubber to hold and transport bulk materials.
Types of bucket elevator
Centrifugal bucket elevator: This is the most common type and is ideal for handling heavy, abrasive materials. Centrifugal force is used to discharge the material from the bucket, making it suitable for smooth and fast processing.
Continuous bucket elevator: This type of elevator is designed for gentle handling of fragile materials. They operate at lower speeds and are often used in the food processing industry where material degradation is a concern.
Positive discharge bucket elevator: Used for materials that tend to stick or are difficult to discharge. They are designed with features to prevent material buildup and ensure smooth discharge.
-
It uses belt as the transmission device, which is suitable for conveying light materials and granular materials, such as grain, feed, etc. It runs smoothly, has low noise and is relatively easy to maintain.
-
It uses plate chain or chain as the transmission device, which is suitable for conveying heavy materials, high-temperature materials or easily abrasive materials, such as cement, coal, limestone, etc. It has a strong and durable structure and is suitable for harsh environments.
-
Arranged in a "Z" shape, it can realize horizontal and vertical transportation, with a low product damage rate. It can unload at a single point or multiple points, and is suitable for material supply for weighing/packaging lines/batch/color sorting.
How does the bucket elevator work?
A bucket elevator works on a simple principle of vertical transportation of bulk materials using buckets attached to a rotating chain or belt. Here is how a bucket elevator typically operates:
Loading: The bulk material to be transported is fed into the buckets at the bottom of the elevator.
Lifting: The buckets are attached to a chain or belt that moves in a continuous loop. As the chain or belt moves, the buckets are lifted vertically.
Discharge: At the top of the elevator, the buckets tip over and unload the material into a chute, conveyor, or another processing system. The material is then carried away for further processing or storage.
Return: After unloading, the empty buckets continue their loop back down to the bottom to pick up more material.
Video
Advantage
Vertical conveying capacity: Compared with horizontal conveying equipment such as belt conveyors or chain conveyors, bucket elevators are more suitable for handling vertical material conveying needs.
Suitable for a variety of materials: Bucket elevators are suitable for various material types, including granules, powders, block materials, etc. Compared with other conveying equipment, bucket elevators are more flexible in handling different types of materials.
Space saving: Due to its vertical conveying design, bucket elevators can save a lot of space, especially suitable for working environments with limited space.
Simple and sturdy structure: The structure is simple and sturdy, the operation is stable and reliable, and the maintenance and failure rate are reduced.
High degree of automation: The elevator can be integrated with the automation system to realize automatic material transportation and control, and improve the automation level of the production line.
project | Vertical Screw Feeder | Vertical Bucket Elevator | Climbing Belt Conveyor |
Floor area | the smallest | smaller | maximum |
Delivery angle | 90° | 90° | Generally used for inclined conveying below 70° |
Delivery capacity | good | excellent | good |
Suitable material | granular or powdery material | Dry bulk material, no special requirements | Parcels and other large-volume products or fruit and vegetable foods, etc. |
Advantage | Small footprint, no dust flying | Capable of substantial vertical lift of 40m | Simple structure, the least cost among similar lifting and conveying products |
shortcoming | Stricter requirements on the materials to be transported | The price is higher, and high-value or large-volume production can achieve the best cost performance | Not suitable for conveying powder or fine particles, not recommended for vertical conveying |
Technical Parameters
Model | Max feed size(mm) | Capacity(T/H) | Lifting speed(m/s) | Belt width(mm) | Lifting height(m) |
TD160 | 25 | 5.4-16 | 1.4 | 200 | <40 |
TD250 | 35 | 12-35 | 1.6 | 300 | |
TD315 | 45 | 17-40 | 1.6 | 400 | |
TD400 | 55 | 24-66 | 1.8 | 500 | |
TD500 | 60 | 38-92 | 1.8 | 600 | |
TD600 | 70 | 85-142 | 2 | 700 |
Bucket elevator structure
Chain or Belt: This is the driving mechanism of the elevator, carrying the buckets up and down. Chains are typically used for heavy-duty applications, while belts are more suitable for lighter loads.
Head Pulley or Sprocket: This component guides the chain or belt around the top of the elevator, changing its direction.
Foot Pulley or Sprocket: This component guides the chain or belt around the bottom of the elevator, changing its direction.
Drive Motor: This provides the power to rotate the chain or belt, lifting the material.
Loading Boot: This is the area where the material is fed into the buckets at the bottom of the elevator.
Discharge Spout: This is where the material is discharged from the buckets at the top of the elevator.
How to choose bucket elevator?
Traction components: plate chain, ring chain and belt types are selected according to the material temperature, humidity, viscosity, particle size, loose density and abrasiveness.
Equipment total height: the lifting height is determined according to the customer's actual foundation conditions and lifting requirements, and then the total height is determined (the total height is the lifting height plus the height of the head and the base)
Drive device: Y series motor + reducer with backstop (motor power exceeds 18.5KW, hydraulic coupling is required)
Bucket speed: bucket speed of high temperature materials and abrasive materials is less than 0.3m/s, and the bucket speed of adhesive materials is 0.5~1.2m/s.
Bucket capacity: calculated by horizontal bucket capacity, generally 0.75%~0.85% of the horizontal bucket capacity is taken to calculate the lifting amount during operation.
Application
Agriculture: used to transport grains, seeds, feed pellets, feed powder and other materials.
Construction materials: used to transport powdered or block raw materials such as cement and limestone.
Chemical industry: used to transport fertilizer raw materials such as urea, amino acids, plastic pellets and other materials.
Mining and metallurgical industry: used to transport raw materials such as coal, ore, metal ore, slag and other raw materials.
Food processing industry: used to transport sugar, sugar pellets, etc.
Packaging industry: used to transport packaging materials, cartons, etc.
Warehousing logistics: used to transport goods to warehouses at different levels.
Solutions by Industry