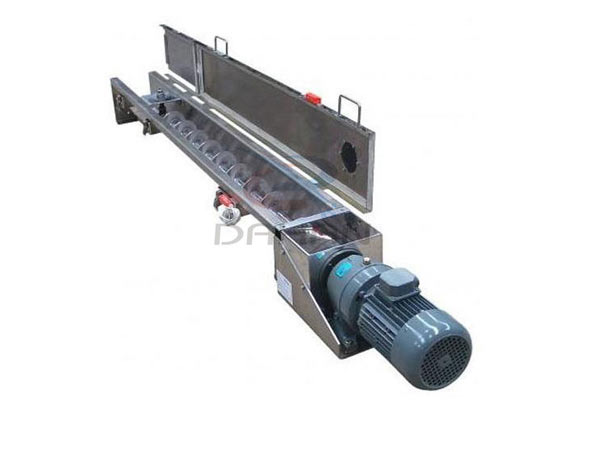
PET flake screw conveyor
It is mostly used in the environmental protection processing industry to transport PET flakes after plastic bottles have been crushed and processed. It is a common transport and transfer equipment in the plastic recycling and reprocessing process.
Spiral diameter: 140-290mm
Conveying length: 30-60 meters
Delivery capacity: 1.4-458 cubic meters per hour
Delivery angle: 0-60°
Motor power: 2.2-30KW
Speed: 240-310r/min
Product introduction of PET flake screw conveyor
PET flake screw conveyor is a screw conveyor specially designed for the transportation and handling of PET flake. PET (polyethylene terephthalate) flakes are small pieces of plastic produced from recycled PET bottles that are often used to make new PET bottles and other products such as textiles and packaging materials.
Screw conveyors are used to transport PET flakes from one stage of the manufacturing process to another. This includes transporting PET flakes from the shredder to the washing line, from the washing line to the drying process, and from the drying process to storage or packaging areas, and can be customized to meet specific requirements.
-
PET Flake Screw Conveyor
Applications
PET flake screw conveyor is used in many applications in PET flake manufacturing. The following are some specific applications of PET flake screw conveyors:
PET bottle production: Commonly used in the production of PET bottles, PET flakes are transported from the cleaning and drying process to the injection molding machine that produces PET bottle preforms.
Textile Manufacturing: For the manufacture of textiles made from recycled PET, PET flakes are transported from the washing and drying process to the extruders that produce textile fibers.
Packaging material production: For the production of packaging material made of recycled PET, the PET flakes are transported from the washing and drying process to the extruders that produce the packaging material.
Industrial Filtration: Can be used in industrial filtration applications where PET flakes are used as the filter media and the PET flakes are conveyed from the cleaning and drying process to the filtration system.
Construction materials: For the production of construction materials made from recycled PET. PET flakes are transported from the washing and drying process to the extruders that produce building materials.
Application advantage
1.Efficient Material Handling: Designed to handle high material handling capacity, enabling efficient transport of large volumes of PET flakes, which increases productivity and reduces production costs.
2.Contamination Control: Screw conveyors for PET flake production are designed with a smooth surface finish and minimal crevices, making them easy to clean and preventing the build-up of debris or contamination. This results in a higher quality product and less waste.
3.Special Coatings: Can be engineered with special coatings or materials to deal with the abrasive nature of PET flakes. This helps prevent conveyor wear, ensuring longer service life and lower maintenance costs.
4.Cost-effective: Relatively low maintenance costs and long service life, reducing the need for frequent replacement or repairs.
5.Customizable Design: Can be customized to meet specific requirements, including feed rate, flow rate and material handling capacity. They can be designed to handle the most challenging materials while minimizing wear, ensuring a long service life.
Video
Screw Conveyor for PET Flake
PET Water Bottle Flakes Screw Conveyor
Product number
Model |
Diameter (mm) |
Pitch (mm) |
Rotating speed (r/min) |
Capacity (m³/h) |
Rotating speed (r/min) |
Capacity (m³/h) |
Rotating speed (r/min) |
Capacity (m³/h) |
Rotating speed (r/min) |
Capacity (m³/h) |
|
Small | 100 | 100 | 100 | 140 | 2.2 | 112 | 1.7 | 90 | 1.4 | 71 | 1.1 |
125 | 125 | 125 | 125 | 3.8 | 100 | 3 | 80 | 2.4 | 63 | 1.9 | |
160 | 160 | 160 | 112 | 7.1 | 90 | 5.7 | 71 | 4.5 | 56 | 3.6 | |
200 | 200 | 200 | 100 | 12.4 | 80 | 9.9 | 63 | 7.8 | 50 | 6.2 | |
Small | 250 | 250 | 250 | 90 | 21.8 | 71 | 17.2 | 56 | 13.6 | 45 | 10.9 |
315 | 315 | 315 | 80 | 38.8 | 63 | 30.5 | 50 | 24.2 | 40 | 13.4 | |
400 | 400 | 355 | 71 | 62.5 | 56 | 49.3 | 45 | 38.6 | 36 | 31.7 | |
Large | 500 | 500 | 400 | 63 | 97.7 | 50 | 77.6 | 40 | 62 | 32 | 49.6 |
630 | 630 | 450 | 50 | 138.5 | 40 | 110.8 | 32 | 88.6 | 25 | 69.3 | |
800 | 800 | 500 | 40 | 198.5 | 32 | 158.8 | 25 | 124.1 | 20 | 99.3 |
product structure
PET flake screw conveyor is mainly composed of inlet and outlet, pipe body, screw blade, reducer and driver.
Inlet and outlet: It can be connected with other feeding or discharging equipment.
Tube body: It is mainly used to load the container of PET flake, and stipulates the forward direction of PET flake.
Spiral blade: The main force that pushes the PET flake forward. The material and thickness of the spiral blade can be replaced and adjusted.
Reducer and driver: provide power for PET flake conveying, and at the same time limit the screw rotation speed through the reducer to ensure conveying efficiency and production safety.
Solutions by Industry
-
PET Bottle Production Plant in Asia
A PET bottle production plant in Asia uses PET flake screw conveyors to transport and handle PET flakes from the washing and drying process to the injection molding machines that produce the preforms for the PET bottles. The plant processes over 10,000 tons of PET flakes per year, producing high-quality PET bottles for the food and beverage industry.
-
Construction Materials Production Plant in North America
A construction materials production plant in North America uses PET flake screw conveyors to transport and handle PET flakes from the washing and drying process to the extrusion machines that produce the construction materials. The plant processes over 2,000 tons of PET flakes per year, producing high-quality recycled construction materials for the building industry.
-
Textile Manufacturing Plant in Europe
A textile manufacturing plant in Europe uses PET flake screw conveyors to transport and handle PET flakes from the washing and drying process to the extrusion machines that produce the fibers for the textiles. The plant processes over 5,000 tons of PET flakes per year, producing high-quality recycled textiles for the fashion industry.