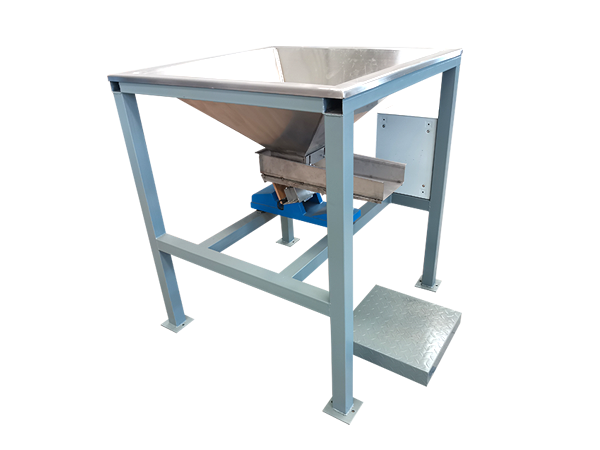
Auto Packing Electromagnetic Vibrating Feeder
It is generally installed at the discharge port of the storage bin. Relying on the gravity of the powder and the light effect of the feeding mechanism, the powder in the storage bin is discharged and continuously and evenly transported to the weighing equipment, and then sent to the weighing equipment. Packing Machine. Function: quantitative feeding, quantitative weighing, quantitative packaging
Capacity:0.1-6T/H
Power: 5-50W
Electric Power Supply: 220V, single phase, 50HZ
Introduction of Auto Packing Electromagnetic Vibrating Feeder
Auto packing electromagnetic vibrating feeder is an indispensable and important part of the powder automatic batching weighing system. It is generally installed at the discharge port of the storage bin. Relying on the gravity of the powder and the forced action of the feeding mechanism, the storage The powder in the silo is discharged and conveyed continuously and evenly to the weighing equipment. In the powder automatic batching and weighing system, both high output, high weighing efficiency and high weighing accuracy are required, which requires the electromagnetic vibrating feeder to control the material flow and play the role of quantitative feeding.
In addition, it is necessary to close the discharge port immediately when the electromagnetic vibrating feeder stops working. Especially when a variety of raw materials with different ingredients and types are required, they can be batched according to the formula and can be accurately weighed. That is to say, the electromagnetic vibrating feeder is required to have both feeding and metering functions.
Features and Benefits
1. Using thyristor half-wave rectifier for power supply, the feeding amount can be adjusted steplessly during use.
2. The feeding port is generally softly connected with the discharging port of the storage bin, and a gate is set on the discharging port of the bin or the chute to prevent the material from flowing out of the bin.
3. It is equipped with an inclined chute, and the rear side plate of the inclined chute is used to bear most of the warehouse pressure.
4. The load cell accurately weighs the product when it is discharged through the processing machine.
Video
Structure and Working Principle
Auto packing electromagnetic vibrating feeder is mainly composed of material trough, electromagnetic vibration exciter and vibration damper. The trough is a bearing member, used to bear the material from the storage bin, and transport it to the weighing equipment through electromagnetic vibration. The electromagnetic vibrator is a component that generates energy for reciprocating vibration in the trough. The function of the shock absorber is to reduce the vibration force transmitted to the foundation or frame, and the feeder is suspended on the wall of the storage bin or on the building components through the shock absorber.
Model | B | B1 | B2 | B3 | L | L1 | L2 | L3 | H | H1 | H2 |
GZV1 | 40 | 60 | 50 | 80 | 200 | 92 | 118 | 273 | 20 | 138 | 152 |
GZV2 | 60 | 80 | 50 | 80 | 300 | 95 | 118 | 274 | 30 | 156 | 168 |
GZV3 | 80 | 110 | 60 | 100 | 400 | 224 | 264 | 480 | 40 | 202 | 217 |
GZV4 | 100 | 130 | 70 | 120 | 500 | 310 | 360 | 568 | 50 | 236 | 256 |
GZV5 | 120 | 150 | 70 | 120 | 550 | 310 | 400 | 630 | 60 | 265 | 295 |
GZVK1 | 400 | 430 | 240 | 300 | 420 | 130 | 180 | 466 | 35 | 200 | 230 |
GZVK2 | 500 | 530 | 320 | 385 | 600 | 240 | 300 | 640 | 40 | 205 | 235 |
Technical Parameter
Model |
Capacity (t/h) |
Feeding particle size (mm) |
Vibration frequency (tim/min) |
Amplitude (mm) |
Power (KW) |
Weight (KG) |
DZV1 | 0.1 | 13 | 3000 | 1.5 | 0.005 | 4 |
DZV2 | 0.5 | 20 | 0.008 | 7 | ||
DZV3 | 1 | 25 | 0.02 | 12 | ||
DZV4 | 2 | 30 | 0.025 | 18 | ||
DZV5 | 4 | 40 | 0.03 | 22 | ||
DZVK1 | 5 | 45 | 0.03 | 27 | ||
DZVK2 | 6 | 50 | 0.06 | 45 |
Application
Auto Packing Electromagnetic Vibrating Feeder is widely used in different fields such as light industry, chemical industry, food, etc. It can be used for small and intermittent production of powder, granular product feeding, quantitative feeding, quantitative automatic packaging and other production processes.
The Auto Packing Electromagnetic Vibrating Feeder can be used for temporary storage of dry, free-flowing food and non-food products to bucket elevators.
It can handle various bulk materials such as food, medicine, industrial products, metal parts, etc., and is mostly used for packaging a small amount of bulk products.
Solutions by Industry
-
Multiple Auto Packing Electromagnetic Vibrating Feeders work together
Mixed Vegetable Dried Production Line
-
Auto Packing Electromagnetic Vibrating Feeder with packing machine
Popcorn Production Line
-
Auto Packing Electromagnetic Vibrating Feeder spreads seasonings evenly over nuts
Nut production line
Use and Installation
Whether the process configuration and installation of the uto packing electromagnetic vibrating feeder in the powder automatic batching weighing system is reasonable will directly affect the performance of the system. In the powder weighing system, the materials that need to be weighed at the same time range from a few to dozens, and the properties of the materials vary widely. To this end, the following points should be noted:
(1) The feeding port of the electromagnetic vibrating feeder is generally softly connected with the discharging port of the storage bin. Excessive silo pressure will reduce the normal operation of the feeder, and the influence of silo pressure on the feeder must be minimized. The usual practice is to control the area of the silo vertically projected on the tank body to be smaller than the discharge port of the silo. The area is within 1/4 of the area, but it may cause the material to rise and arch in the storage bin; another method is to configure an inclined chute, and use the rear side plate of the inclined chute to bear most of the warehouse pressure, as shown in Figure 2 Another method is to set a butterfly valve at the discharge port of the silo, and rely on the valve plate of the butterfly valve to bear part of the silo pressure.
(2) In order to adjust the thickness of the material layer in the feeding trough or prevent the material from flowing out of the silo when overhauling the feeder, a gate should be set at the discharge port or chute of the silo. When the silo is fed, the material is flushed out along the feeder, the silo is not allowed to be unloaded, and a material level gauge should be set at the lower part of the silo to ensure a certain amount of material. If the silo is unloaded due to material change or other reasons, the gate should be closed when feeding again. Adjusting the opening of the gate at the discharge port of the silo can increase or decrease the thickness of the material layer in the trough to achieve the purpose of adjusting the feeding capacity.
(3) Whether the selection of the inclination angle is suitable or not when installing the electromagnetic vibrating feeder has a great influence on the feeding capacity and weighing accuracy. If it is inclined downward by 10°, the feeding capacity can be increased by about 30% compared with the horizontal position, but it is also possible that the self-flow is caused by the increase of the sliding of the material, and it is difficult to ensure the weighing accuracy. Therefore, it should be determined according to the nature of the material whether it is inclined upward, downward or horizontal. In addition, adding a flap valve at the discharge port of the feeder can close the flap valve at the end of weighing and stop feeding, so as to avoid blanking at the outlet of the feeder.
(4) The electromagnetic vibrating feeder should be installed as a whole. During installation, it is not allowed to consolidate any rigid accessories on the feeder, and there should be a certain space around it, so that the feeder does not collide with other equipment when it is working. The space in the length direction of the feeder is generally at least 50 mm, and the width in the width direction is generally 25 mm.
(5) The horizontal direction of the feeder after installation should be in a horizontal state to prevent the material from shifting to one side when the feeder is working.